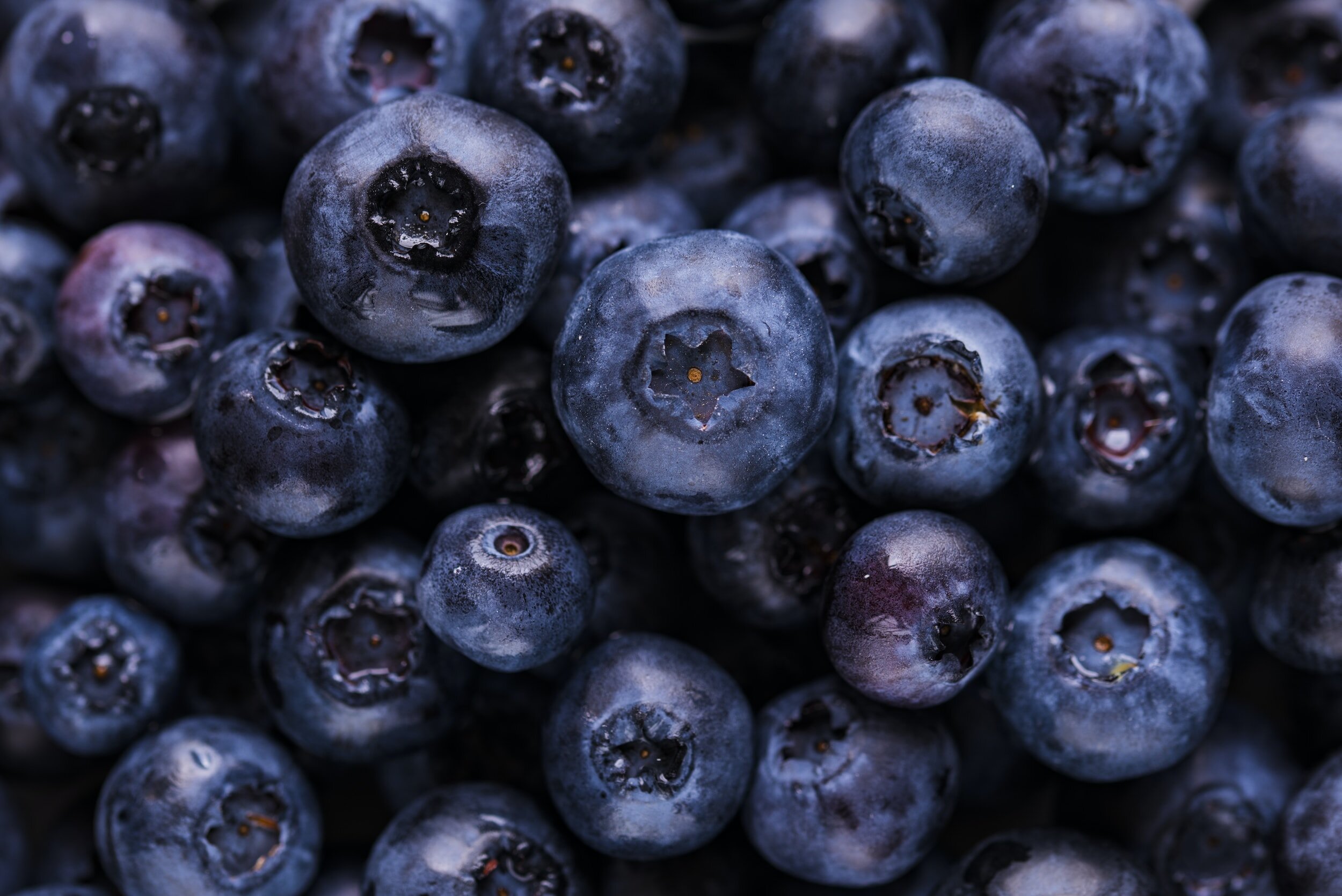
FRUIT & VEGETABLE
CMP designs and manufactures hygienic food processing equipment with a single goal in mind, to keep food safe. We are often involved in the initial stages of the project, providing engineering assistance with overall layouts and arrangements down to detailed engineering discussions on design and approach for the entire process line. Our solutions are often coupled with FPS spiral and IQF tunnel freezers, including turn-key controls and automation. We incorporate equipment from other leading OEM’s to offer complete processing lines.
Some of our product solutions include hoppers and conveyors, even flow bins, add back systems, tote dumpers, augers, cleaning equipment, sorters, ozone wash conveyors, sanitary conveyors, FRS fluid removal systems, glazing conveyors, scale decks, catwalks, and packaging equipment.
CMP provides sound technical advice, project management services, and hygienically designed process equipment to meet the needs and specifications of our customer.
CASE STUDY
CASE STUDY
End-to-End Solutions:
High Volume
Pea Freezing System
Challenge
1/ Sweden based pea producing enterprise specializing in sustainable pea production
2/ Target: 180 tonnes per day of finished frozen peas
3/ Looking for hygienic and reliable freezing system
Solution
1/ State-of-the-art FPS IQF Tunnel Freezer that included sequential defrost and industry best Clean-In-Place (CIP) system.
2/ CMP Fluid Removal System (FRS) to maximize freezer performance and increase product quality.
Result
1/ Customers expectations on sanitary design and hygienic build were exceeded.
2/ Production reached a maximum of 260 tonnes, with a daily average of >200 tonnes.
3/ Customer testimonial: “More production, less cleaning – that was our goal for the new line!”
CASE STUDY
End-to-End Solutions:
Blueberry Processing
Plant - Complete Line
Challenge
1/ Major Atlantic Canada blueberry processor.
2/ Complete line required for greenfield blueberry cleaning, freezing, and packaging line.
3/ Customer looking for one-stop solution provider.
Solution
Complete Line including layout, design, fabrication of equipment, testing prior to shipping, full mechanical installation, and commissioning and start-up support for the new facility.
Result
1/ Blueberry line to accept and clean up to 20,000 lbs. of wild blueberries per hour for freezing.
2/ All equipment for post-freezing, conveyance, destemming, mechanical sorting, laser sorting, visual inspection, and tote and case filling.
3/ Customer extremely happy with the new plant.
CASE STUDY
End-to-End Solutions:
Vegetable Glazing System
After IQF Freezer
Challenge
1/ Required improvement in percent water pickup on glazing of IQF broccoli from less than 3% percent to greater than 8%.
2/ Past glazing concepts did not perform.
Solution
1/ Develop glazing conveyor to provide options of waterfall or spray bar dosing of water onto product.
2/ Bias Shaker to ensure uniform bed.
Result
1/ Greater than 8% of water pickup achieved.
2/ Complete system performing above customers expectations. Equipment is reliable, safe, and easy to maintain.
CASE STUDY
End-to-End Solutions:
Vegetable IQF Freezer Infeed Dewatering
Challenge
1/ Required improvement in production throughput of two FPS IQF freezers installed.
2/ Current dewatering system was underperforming.
Solution
1/ CMP FRS stand alone Fluid Removal System and Bias Shaker added to both lines on feed to tunnel.
2/ CMP FRS Plenum ONLY solution also added to the FPS tunnel under the belt at infeed.
Result
1/ Dewatering results best in class : approximately 1% surface water fed to tunnel.
2/ Production rate increase to 26,000 pounds per hour achieved.
3/ Customer extremely happy.
CASE STUDY
End-to-End Solutions:
Thermodrive Cranberry
Conveyor
Challenge
Cranberry processor requires a sanitary conveyor by-products (cranberry press cake) conveyance. Tight footprint and must incline product. Conveyor will be fed from the press chute and will feed a mobile hopper. Conveyor portable on casters for access and flexibility.
Solution
Sanitary HSS frame style conveyor with UHMW product containment sides to ensure the conveyor is rigid for mobility, yet easy to clean. Intralox ultra-hygienic Thermodrive 8050 belt and stainless steel motor and gearbox.
Result
Ultra-hygienic design and fabrication including the ability to remove the belt in one piece (endless). Drip pans, removable infeed hopper, removable components without tools, hinged side guides for easy cleaning. Final product is a sanitary design show piece.