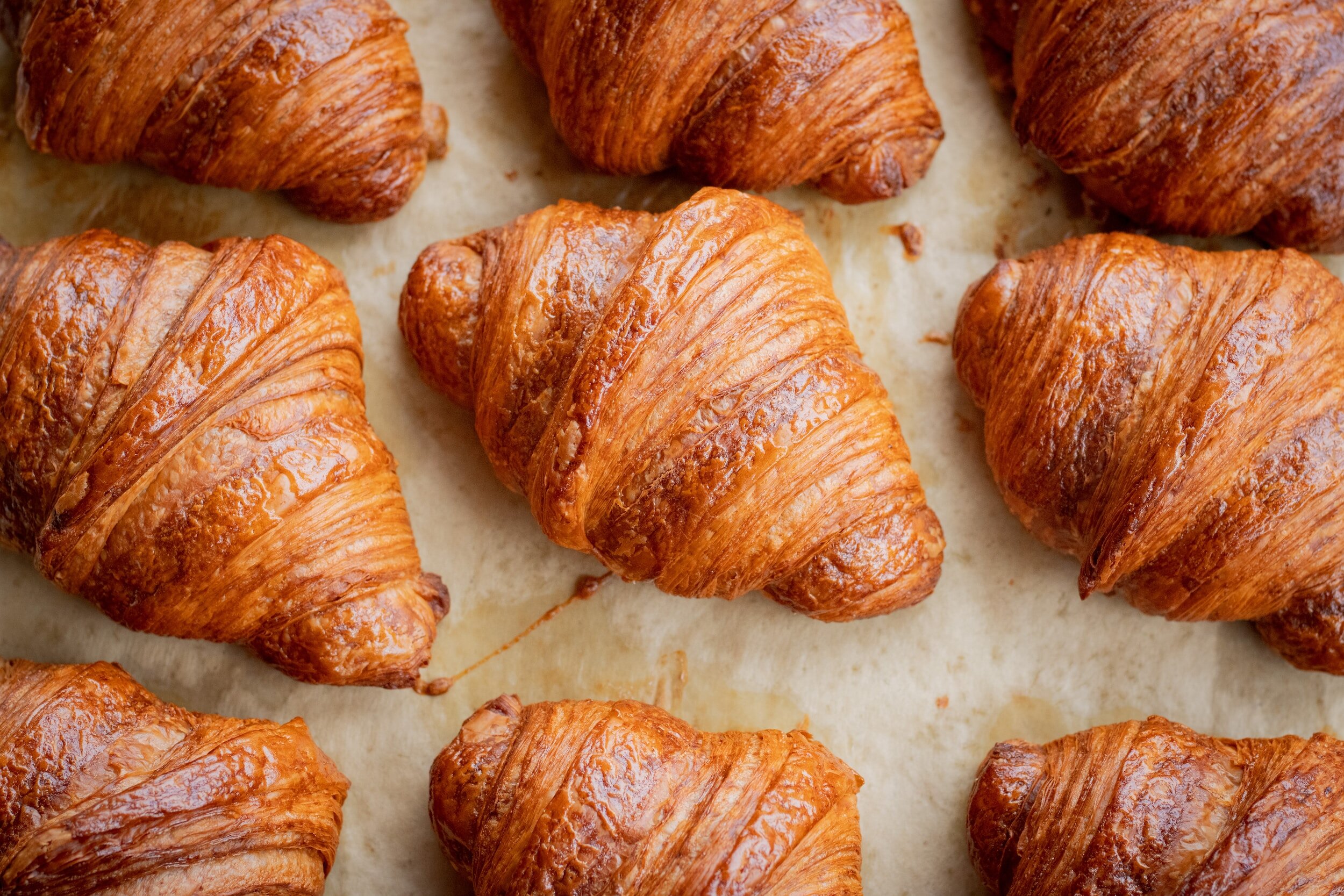
BAKERY
Gone are the days of dusting, scraping, and spot cleaning bakery equipment. Times have changed. Informed bakers are elevating their standards, recognizing the importance of hygienic design, and choosing suppliers such as CMP focused on food safety, as their new key purchase drivers. Sanitation in the bakery industry is no longer a luxury, it is a necessity.
We see our competition building “today’s bakery to yesterday’s standards”. At CMP and FPS, we build “today’s bakery to tomorrow’s standards”.
CASE STUDIES
CASE STUDY
Sanitary Spirals:
The World’s Widest
Ambient Spiral Belt
Challenge
US-based customer needs to cool fresh baked cookies transferring out of an elevated oven transfer conveyor that is 64” wide. Minimal floor space available. Variable belt speed required. Must be hygienically designed and built.
Solution
Intralox DDS Direct Drive Spiral System – FPS/CMP is the ONLY OEM in the world authorized to purchase, design, and build spiral solutions with belting wider than 60” – up to 72” wide. This is the second sanitary ambient spiral for this customer.
Result
Another successful project for FPS/CMP. Customer up and running and in full production as planned! This is officially the widest belt in the world installed and running on an ambient spiral for the bakery industry.
CASE STUDY
Sanitary Spirals:
Side Drive Spiral
Lowerator
Challenge
US-based customer needs to lower packs of sausages from 10’ TOB coming out of the FPS SIS Chilling System down to 3’ TOB prior to the packing system. In addition to lowering the product in a small footprint, the product must be blown-off to remove surface water.
Solution
Intralox SideDrive Sanitary Spiral; fully washdown, cost effective, and hygienic. A custom integrated blow-off cabinet with floor mounted blower cabinet removes surface water. A final split conveyor was added to spread the product to two check-weighing units.
Result
The customer is operating at full capacity with better than expected results. Product is handled with care and blow-off system is working well. Customer has been pleasantly surprised with the minimal maintenance required for this unit and the robust quality of the unit.
CASE STUDY
End-to-End Solutions:
Wide Format
Smart Depositor System
Challenge
Replace an existing problematic conveyor system used to transfer 19 rows of baked patties long side leading into 6 lanes, short side leading to feed an existing freezer. Product orientation and equipment reliability are both critical.
Solution
Turnkey solution complete with 10’ wide tight-transfer conveyors to ensure smooth transition from the band oven. 6 position, Wide Format Smart Depositor transfer onto ultra-hygienic take-away conveyor to freezer.
Result
System fully wired and fully tested in-house using customer provided product at full production rate. Full installation, commissioning, and start-up support by CMP. Customer is running at full production and their expectations were exceeded.