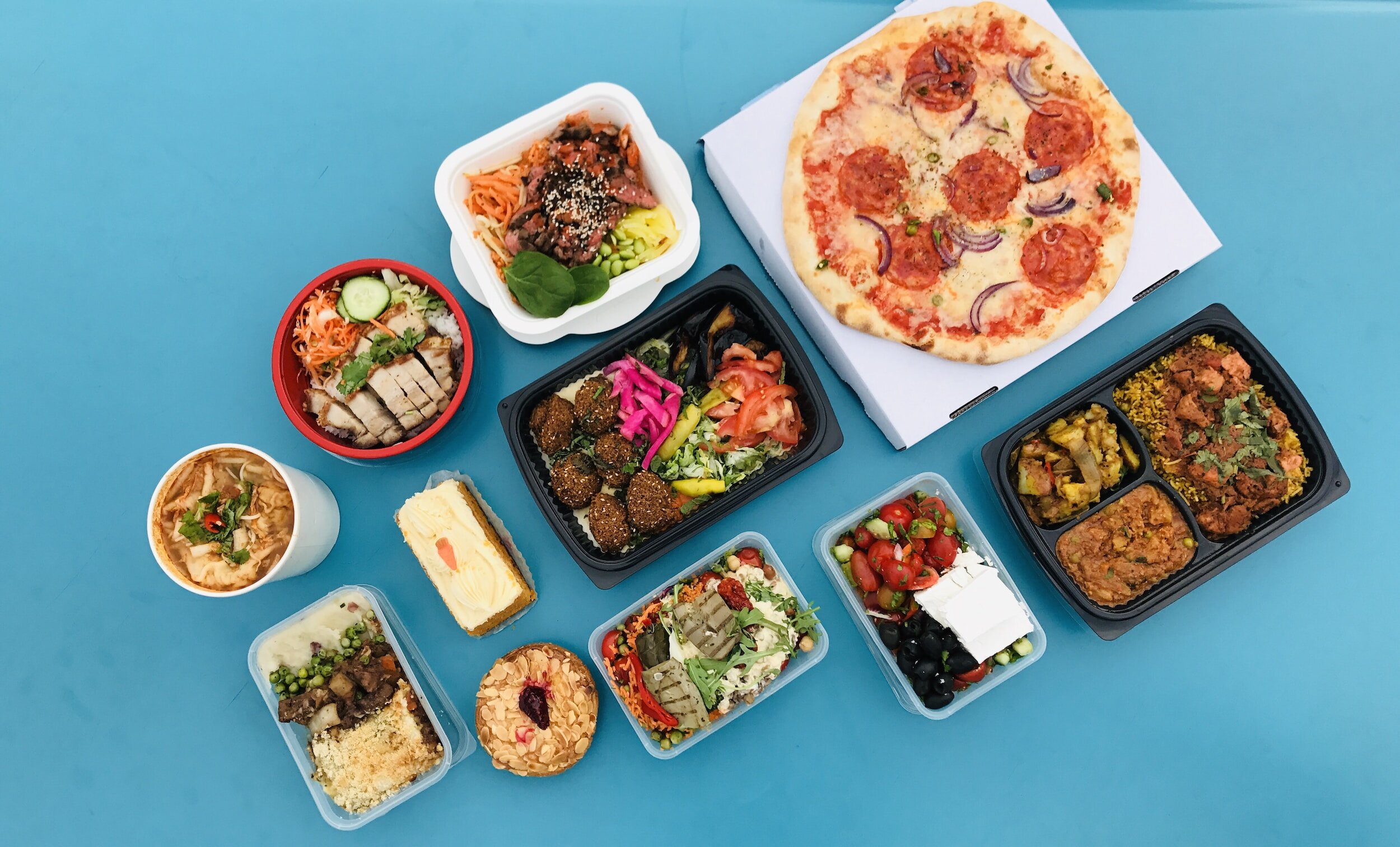
PREPARED FOOD
From pizza pockets to gyoza, from rice to tacos and burritos, from bags of taco sauce to trays of mashed potato, from frozen pizza to RTE single serve meals; CMP designs and manufacturers high quality hygienically designed equipment for the prepared foods market.
We specialize in hygienic conveyors, tote handling systems, sanitary decks, smart merge, diverge, pull back depositor and sorting solutions. Our solutions are often coupled with FPS spiral and tunnel freezers, including turn-key controls and automation. We incorporate equipment from other leading OEM’s to offer complete processing lines.
Bring us your product handling challenge and layout constraints and we will get to work on a custom solution for you.
CASE STUDIES
CASE STUDY
End-to-End Solutions:
Freezer Discharge Controlled
Tote Filling System
Challenge
The world’s largest food and beverage company looking to source an automated system to transfer and weigh frozen meat portions into staged combos. Highest hygienic standards for this RTE product and full integration with customer’s digital inventory management system.
Solution
Turnkey solution based on industry proven product handling, portioning, weigh system, and controls. Compact design complete with integrated catwalks and decks for easy cleaning, inspection, and operator access. Sanitary design and construction using the most hygienic belting in the industry.
Result
Successful collaborative project between customer and CMP project execution teams. State of the art controls and safety systems. Throughput target of 7200 lbs./hr. exceeded. System is up and running and working well. Customer happy to know CMP is a supplier they can call on for future projects.
CASE STUDY
End-to-End Solutions:
FPS Freezer
Discharge Conveyor
Challenge
A high-quality ingredient food producer in the Southern US specializing in Hispanic foods purchased a new FPS spiral freezer and needs a hygienic solution to transfer their frozen packaged products from the 21’ discharge height down to 5’ in a small footprint.
Solution
Using the latest technology in hygienic belting from Intralox, a 44” wide ThermoDrive belting conveyor transfers over 7000 frozen packages an hour. A custom chute from the FPS freezer to the decline conveyor ensures smooth and controlled product transfer.
Result
Customer delighted with solution given the tight floor space that was available. Customer extremely happy with the sanitary design and ease of cleaning on this difficult application. Another successful project and collaboration with a great customer, Intralox, and FPS + CMP!
CASE STUDY
Product Handling Innovation:
High-Speed Pizza
Packaging Lines
Challenge
A high quality and high-volume pizza producer in Illinois looking for a completely new packaging area to increase their throughput (up to 200ppm) and remove an outdated, difficult to clean and maintain slip-torque roller conveyor system. New system must be hygienic.
Solution
Using the tight existing packaging area a new sanitary conveyor transfer system for 2 Lines complete with full integration of the existing cartoners, inspection equipment, brand new high-speed case packer, new labeler. Special dual-belt turners included to turn packs and cases.
Result
Designed in collaboration with all the other vendors and the customer’s team. Full controls provided by CMP included a remote HMI station for easy operator use. Customer running at full capacity and cleanability of the system exceeded expectations. A successful turnkey project for client and CMP!
CASE STUDY
Product Handling Innovation:
Custom AIM
Narrowing System
Challenge
Well established and beloved Pizza producer based in the Midwest US adding a new process to their line and needed a custom solution to ‘narrow’ two lanes of pizzas to fit into their new pre-melter. Top priorities are hygienic design and ease of cleaning.
Solution
No standard Intralox AIM solution available that would meet the customer’s exact dimension requirements. Custom hygienic AIM narrowing solution created to incorporate two mirrored AIM SWITCH units into one frame with one drive shaft.
Result
The first of its kind! Installed and performing perfectly. Easy to clean design and robust build. All parts are standard components, readily available and easy to source and maintain. Customer happy with the partnership and collaboration between themselves, CMP, and Intralox to complete this successful product handling innovation project.
CASE STUDY
End-to-End Solutions:
IQF Burritos -
Freezer Discharge
Challenge
US based, high quality ingredient burrito producer looking for a hygienic conveyance solution for 6,000 lbs./hr. System to include infeed to new freezer and discharge of IQF burritos from the top of a spiral freezer to packaging. Complete with turnkey controls.
Solution
CMP H3 Hygienic Series Conveyors for both Infeed and Discharge of Freezer. Heavy duty construction with easy to clean design, made for RTE direct food contact. Custom controls complete with highspeed retract to change product orientation. Full FAT with product at CMP prior to installation by CMP.
Result
Complete Line performing above expectations. Customer impressed with how robust and hygienic the conveyors are. Customer very happy with the professionalism and high level of customer service on the project. Two additional orders placed by this customer since completion of this project.
CASE STUDY
Hygienic Conveyors:
Cooked Rice
Transfer System
Challenge
Transfer 18,000lbs./hr. of cooked rice from the auger cooker into a shared flume tank. Rice at 200°F in uneven dumps of between 10-50lbs at 6 dumps per minute. Each discharge contains approximately 10 gallons of hot water to be captured and re-used.
Solution
Two identical wire mesh transfer conveyors complete with custom designed infeed hopper to receive random amounts of rice from the auger cooker. Hot water collection tanks below conveyors and two identical heavy duty SS Shakers.
Result
Customer delighted with robust construction and production results. Water collection tank works as intended and rice flows smoothly from the auger cooker to flume tank. Customer asked for proposal of 5 additional CMP SS Shakers.
CASE STUDY
Tote Handling Systems:
Stainless Steel
Two-Stage Tote Dumper
Challenge
US-based customer requires a dumper to unload combo boxes of RTE dry products seated on wooden pallets. The new dumper must be able to be floor loaded with a manual pallet jack, a clear dump height of approximately 64” from the floor, and capable of handling loads up to 2,200 lbs.
Solution
Two Stage Tote Dumper, all stainless-steel construction. Two Stage function will ensure that only the combo box and product will be above the receiving hopper (food zone). When a pallet and combo box have been loaded, the operator will activate the dump sequence from a SS control panel.
Result
System tested in-house using fully loaded combos at maximum weight and maximum rate. Dumper operates smoothly and consistently. Customer ordered 2 additional identical units as a result of this successful project!
CASE STUDY
End-to-End Solutions:
Frozen Flavored Rice
Production Line
Challenge
New production line for 4,000 pounds per hour IQF frozen flavored cooked rice. The new line required incorporating best in class hygienic design throughout the system from rice soak tanks, through to cooking, ingredient addition, IQF freezing and bagging line.
Solution
Delivered an end-to-end complete line solution including rice soak tanks, hygienic process conveyors, FPS IQF Freezer, equipment stands, sanitary process decks, catwalks, special spreader system for feed to FPS IQF, and sanitary scale deck system.
Result
Customer delighted with significant improvements made to hygienic design compared to existing lines. Installation was very smooth with no re-work required on site due to detailed 3D process modeling utilized in the engineering phase.