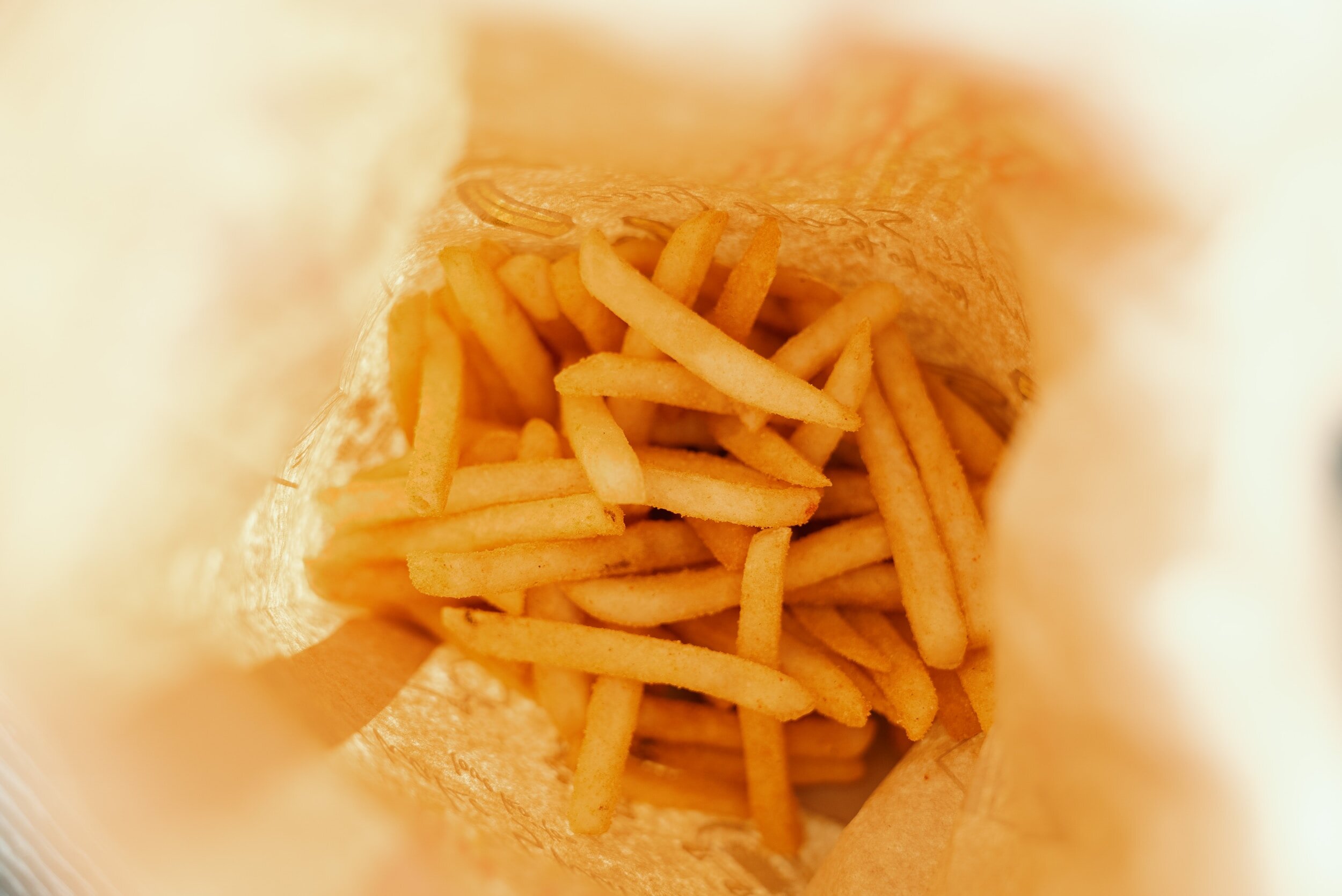
POTATO & FRENCH FRY
At CMP, we know potato processing equipment – we grew up with the industry on our door step. As part of the FPS family we can deliver total plant solutions from raw receiving through to packaging for French fry, potato chip, and a host of specialty potato products.
Raw receiving, hygienic process conveyors, equipment stands and decks, and process area equipment including blanchers, dryers, fryers, and freezers are our core specialty working together with FPS and GEM Equipment (part of the FPS Family). We have strategic relationships set with several other OEM’s which have enabled our End-to-End complete process line integration capability.
Some of our additional product solutions specific to the potato industry include receiving hoppers and storage bins, all types and sizes of hygienic conveyors, even flow surge bins, add back systems, tote dumpers, augers, batter mix systems, SAPP dosing systems, flume transport, scale decks, catwalks, mezzanines, and more.
CASE STUDIES
CASE STUDY
End-to-End Solutions:
Potato - Frozen
Grading Line
Challenge
US based potato products producer looking for ultra-hygienic frozen french fries grading system for 25,000lbs./hr. System to include all conveyors, shakers, a bypass system, access stand, and controls. To be integrated with a KEY Optical Sorter.
Solution
Compact footprint. ThermoDrive ultra-hygienic belting conveyors, heavy-duty bias shaker feed to the Sorter, bypass system, and complete integrated controls. Design, Manufacture, Install, and Commission of complete Line.
Result
Customer’s expectations exceeded on hygienic design and manufacture. Production rates achieved, system running smoothly. Integration with KEY Optical Sorter both mechanically and controls completed successfully. Customer happy with grading system functionality and cleanability.
CASE STUDY
End-to-End Solutions:
Freezer Discharge to
Metal Detector
Challenge
US based potato products producer looking for ultra-hygienic transfer system for 5,000lbs./hr. of IQF hashbrowns and tater tots. System to include all conveyors, accumulation, weigh scale, bagger, abort chute, and sanitary scale deck.
Solution
Seamlessly integrated solution to receive products from the FPS Spiral Freezer. ThermoDrive ultra-hygienic belting conveyors, Accumulation System, Fastback Shaker, Ishida Scale, and Triangle Bagger. Complete turnkey project including installation.
Result
Customer’s expectations exceeded. Robust construction and easy to clean design. Production rates achieved, system running smoothly. Customer has since placed orders with CMP for another large project and the Add-back System for this Line. A win for both CMP and this valued customer.
CASE STUDY
End-to-End Solutions:
Batter Mix System for Frozen French Fries
Challenge
A batter mixing, hydration, and dosing system was required for a new 25MT frozen French fry line. The mix system must be capable of processing high solids batters greater than 45% solids with varying spices and ingredients addition.
Solution
Working with GEM Equipment (member of the FPS family) we delivered an end-to-end complete line solution including dry powder handling, screening, LIW feeder, shear mixer, mix tank, hydration tanks, holding tanks, cooling system, applicator conveyor and batter blow off conveyors.
Result
Customer delighted with hygienic design, yield, and production rate achieved. Complete integration of the system into the existing GEM fryer complete with a batter bypass system was an added bonus.
CASE STUDY
End-to-End Solutions:
Potato Raw Receiving System
Challenge
A potato processor in South America needed a new raw receiving and storage system to manage potato handling from multiple types of offloading for an 18MT French fry plant. For maximum life and durability, stainless steel construction was requested.
Solution
Delivered an end-to-end complete line solution including truck tipper, 100MT even flow storage bins, length and diameter sizing, washing, mud collection, conveyance, platforms, and a fully automated control system.
Result
Customer delighted with significant improvements made to hygienic design compared to existing lines. 3D process modeling was utilized in the engineering phase to ensure smooth installation and start up.
CASE STUDY
End-to-End Solutions:
SAPP Mix and
Dosing System
Challenge
Customer wanted to change two French fry lines to incorporate a SAPP mix system and flume dosing system to replace manual dosing system used at the blanching phase. Reduction in chemical cost and improvements in SAPP application was the main driver.
Solution
Delivered an end-to-end complete line solution including ergonomic SAPP mix system, custom covered flume delivery system with access deck for sanitation crew.
Result
Significantly reduced chemical usage while improving the ergonomic handling of dry ingredient. Lower concentration SAPP solution was used based on retention time improvement with the addition of the SAPP flume delivery system.
CASE STUDY
Tote Handling Systems:
Driven Tote
Dumper
Challenge
Large Potato Processing customer looking for an animal feed bin loading system to distribute into a 35’-0” long animal feed trailer. The system is to include a side-loaded tote dumper that is manually loaded with a forklift, and a rail system for the dumper to travel on.
Solution
Sanitary designed, heavy-duty construction, elevated tote dumper with a 4,000 lbs. dumping capacity. All stainless-steel materials complete with hydraulic power pack and variable speed electric drive system for positioning. Complete controls, fully wired and testing prior to shipping.
Result
Customer very happy with performance, build quality, and cleanability. During the project, an industrial magnet was built into the design of the dumper for product safety, and a Keyence, industry-best, operator safety system was installed and integrated into the controls system.